Streamlining Reverse Logistics for a Leading Direct-Selling Company
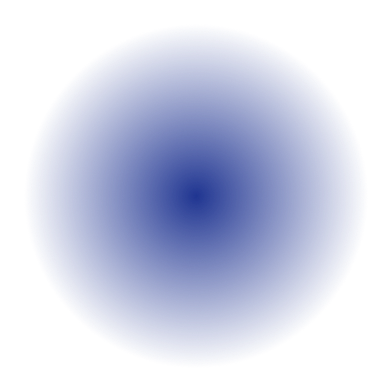
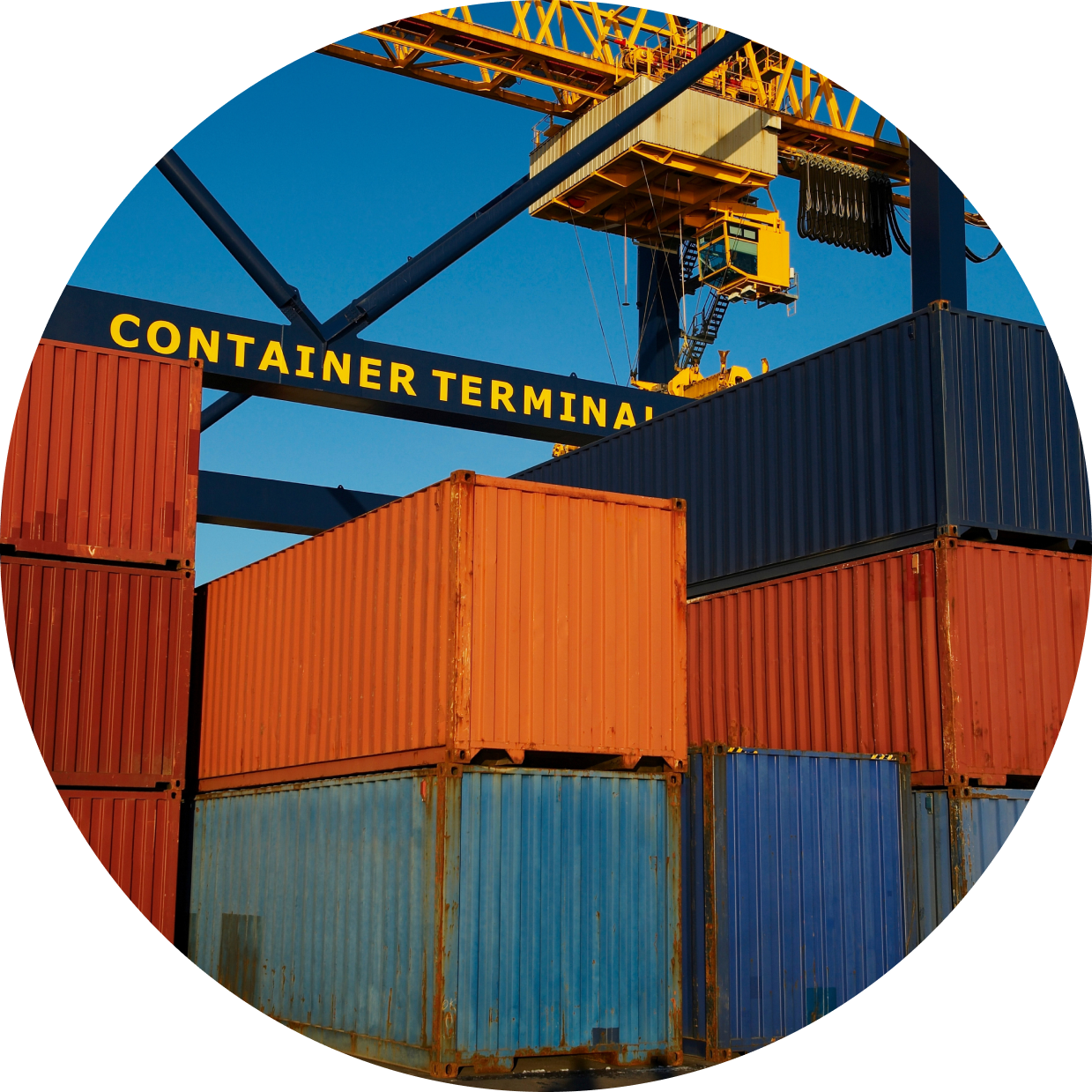
Challenge:
A well-established direct-selling company was managing its entire reverse logistics returns process in-house at a 25,000-square-foot distribution center, staffed by nearly 20 tenured employees. While experienced, the labor costs were high, and the returns process was inefficient—taking up to 3–4 days to complete.
This delay affected Independent Businesses, who relied on timely credit processing. The company needed a cost-effective and efficient solution to improve reverse logistics return processing without sacrificing service quality.
What is the Reverse Logistics Definition?
Reverse logistics refers to the systematic process of managing the backward flow of goods, materials, or products from the end user back to the point of origin or another designated location. The purpose of reverse logistics is often to handle returns, recycling, refurbishing, or proper disposal of products. By implementing an effective reverse logistics strategy, businesses can minimize waste, recover value from returned items, and enhance customer satisfaction through streamlined returns and repairs.
What is Reverse Logistics Returns Processing Optimization?
Reverse Logistics Returns processing optimization focuses on streamlining operations, reducing costs, and improving turnaround times. By outsourcing or restructuring return management, businesses can:
- – Reduce warehouse space requirements.
- – Lower labor costs while maintaining productivity.
- – Improve efficiency, ensuring faster credit processing for customers.
Why Is Fast and Efficient Reverse Logistics Returns Processing Important?
For direct-selling companies, return processing delays impact customer trust and financial operations. An optimized system ensures:
- – Faster refund processing, improving satisfaction among distributors and customers.
- – Lower operational costs through efficient labor allocation.
- – Improved warehouse efficiency, eliminating wasted space and resources.
Our Solution:
Supply Chain Solutions (SCS) redesigned the company’s logistics management system and became the company’s reverse logistics provider, relocating operations to its Grand Rapids facility for a more streamlined, cost-effective solution. Key improvements included:
- – Optimized Warehouse Space: Reduced footprint from 25,000 square feet to 5,000 square feet without sacrificing efficiency.
- – Workforce Efficiency: Cut staff from 20 employees to 7–8, offering fair, sustainable wages while maintaining productivity.
- – Accelerated Processing Time: Reduced return processing from 3–4 days to just 1 day, ensuring IBOs received credits quickly.
Results:
The return process transformation delivered measurable benefits:
- – 80% Reduction in Warehouse Space Usage – From 25,000 sqft to 5,000 sqft.
- – Significant Labor Cost Savings – Reduced workforce while maintaining performance.
- – 75% Faster Processing Time – Cut returns processing from 3–4 days down to just 1 day.
Best Practices in Reverse Logistics Returns Processing Optimization:
To maximize efficiency and reduce costs, companies should:
- – Optimize Warehouse Footprint: Only allocate space based on actual operational needs.
- – Right-Size Workforce Allocation: Maintain a lean, high-performing team to reduce excess labor costs.
- – Automate and Streamline Workflows: Implement technology to track, approve, and process returns efficiently.
- – Prioritize Customer Experience: Ensure refunds and credits are processed quickly to maintain customer trust.
Why Supply Chain Solutions?
The company partnered with Supply Chain Solutions for its expertise in returns processing optimization and warehouse efficiency. Our approach provided:
- Proven Space & Cost Reduction Strategies – Dramatically lowered warehouse footprint and labor expenses.
- Faster, More Reliable Processing – Ensured timely refunds to improve customer and distributor satisfaction.
- Scalable, Industry-Specific Solutions – Designed to meet the unique needs of direct-selling businesses.
Learn More:
Looking to reduce costs and improve your returns processing efficiency? Contact Supply Chain Solutions today to learn how we can help streamline your operations.
Frequently Asked Questions:
What does a reverse logistics expert do?
A professional in returns management focuses on optimizing the handling of returned goods, streamlining processes, and recovering value from returned products. Their expertise ensures efficiency and cost reduction in the supply chain.
Where does reverse logistics impact the supply chain?
The process of handling returns affects inventory management, transportation, and recycling workflows within the supply chain. Efficient handling reduces waste and ensures smoother operations overall.
Why is reverse logistics important?
Managing product returns is essential for reducing waste, recovering resources, and enhancing customer satisfaction. It also helps businesses save costs while maintaining eco-friendly practices.
What is reverse logistics technology, and why is it essential?
Technology for returns handling involves systems that automate tracking, sorting, and processing. Such solutions improve accuracy, reduce manual errors, and make operations more efficient.
What challenges do reverse logistics companies face in the USA?
Handling high return volumes, compliance with regulations, and managing costs are common issues faced by companies specializing in returns management in the United States. Addressing these challenges ensures smoother workflows and sustainability.
How does customer service play a role in reverse logistics?
Efficient service during returns processing ensures timely refunds and clear communication, fostering trust and satisfaction among customers. It’s a key component of maintaining loyalty.
Can you provide a reverse logistics example?
A consumer electronics company might refurbish returned devices and resell them, minimizing waste and recovering value. This approach highlights the importance of efficient returns workflows.
How is procurement impacted by reverse logistics?
Returned items can be reintegrated into inventory, reducing the need for new purchases. This helps businesses save costs and optimize their procurement strategies.
What role do reverse logistics providers play in the supply chain?
Specialized providers handle returned goods efficiently, offering services like recycling, refurbishment, and disposal. Their expertise helps businesses focus on core activities while optimizing costs.
What are reverse logistics metrics, and why are they important?
Performance indicators like return rates and processing times help measure the effectiveness of handling returns. Tracking these metrics ensures continuous improvement and cost savings.
How have reverse logistics companies evolved over time?
Returns management has shifted from manual operations to automation and data-driven decision-making. This evolution has improved efficiency and reduced costs over the years.
Why is benchmarking in reverse logistics crucial?
Comparing returns management performance with industry standards helps identify areas for improvement, ensuring better efficiency and customer satisfaction.
What makes reverse logistics solutions effective?
Streamlined workflows and technology integration ensure that returns are handled efficiently while minimizing costs and environmental impact.
Are there specialized reverse logistics companies in the USA?
Yes, several companies specialize in handling returns for industries like consumer electronics and pharmaceuticals, providing tailored solutions for unique challenges.
Why are returned goods critical in the supply chain?
Returned items can be repaired, refurbished, or recycled, reducing waste and recovering value. Proper handling ensures minimal losses and optimized inventory management.
What is the importance of reverse logistics in consumer electronics?
Efficient workflows ensure that returned devices are refurbished or recycled, reducing environmental impact and operational costs while maintaining quality standards.
How do companies optimize their reverse logistics workflows?
By automating processes and using performance metrics, businesses streamline operations, reduce costs, and enhance overall efficiency.
Why is the importance of reverse logistics growing in today’s market?
With increased customer expectations and environmental concerns, efficient handling of returns has become vital for cost savings and competitiveness.
Need Expert Logistics Advice?
Let’s optimize your supply chain for growth. Reach out to our experts today.
- contact@scsolutionsinc.com 616.554.8900 ext. 101
- Shipment Tracking tms@scsolutionsinc.com