Optimizing Supply Chain Efficiency with an Advanced Inventory Management System
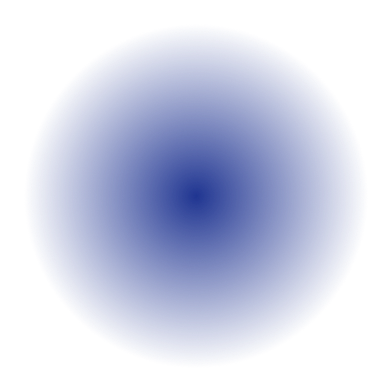
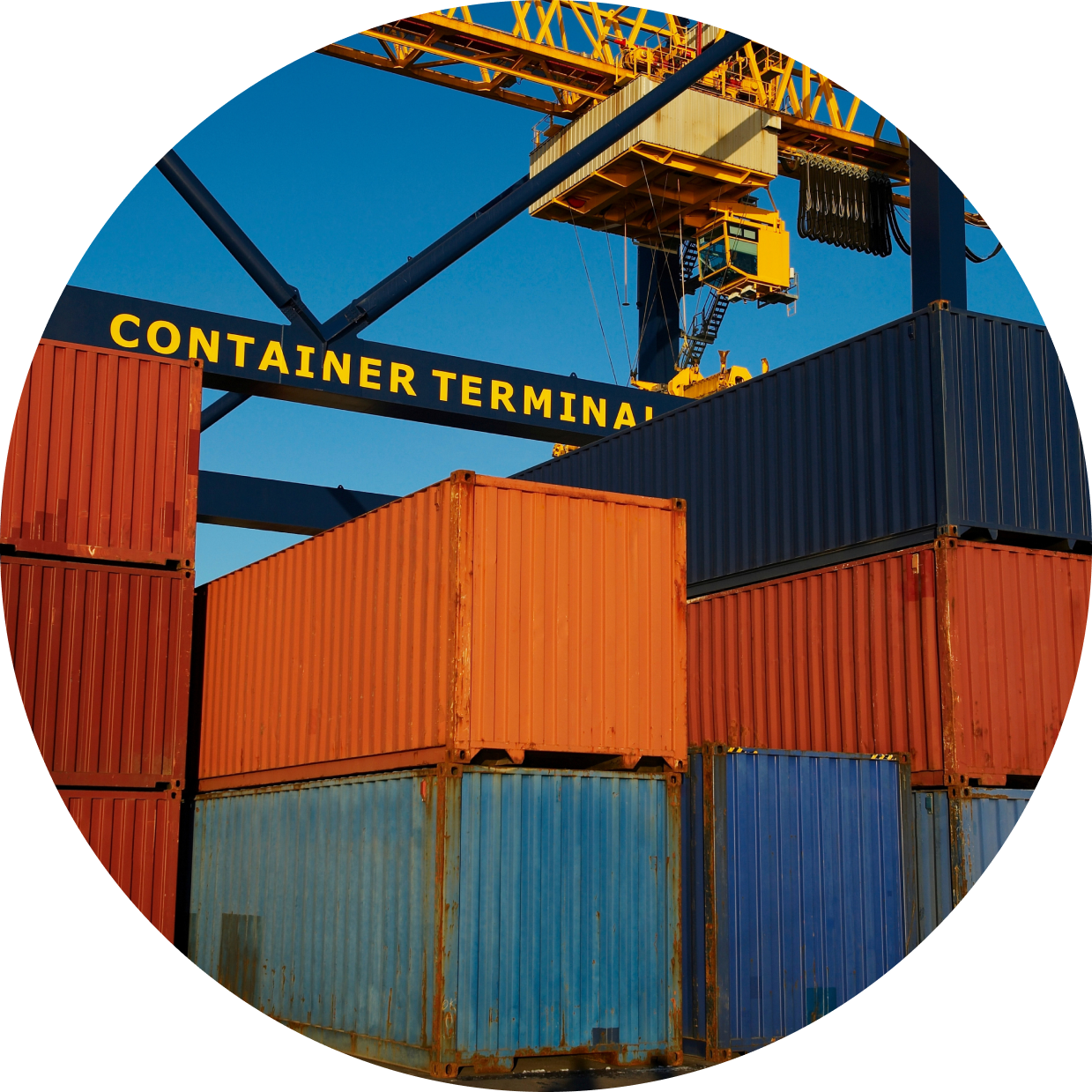
Challenge: Lack of Real-Time Inventory Visibility
An engineering research client faced significant challenges due to a lack of real-time inventory visibility. Their existing inventory management system was outdated and failed to provide accurate insights into inventory levels. This led to delays in the production process, longer lead times, and strained supplier relationships. As a result, costs increased, and delivery times for materials were extended, creating inefficiencies across their supply chain.
Action: Transforming the Inventory Management Process
Supply Chain Solutions was brought in to address these inefficiencies and revolutionize the client’s inventory management in the supply chain. The team conducted an in-depth assessment and implemented a cutting-edge warehouse inventory management system. This solution included the following key actions:
- Real-Time Inventory Visibility: A new inventory management system was introduced to provide immediate insights into inventory levels, enabling better decision-making.
- Order Fulfillment Consolidation: Operations were streamlined by consolidating order fulfillment into a single facility, improving efficiency and reducing redundancies.
- Cross-Department Synchronization: Efforts were aligned between the Domestic and Warehouse departments to enhance the overall inventory management process.
Result: Enhanced Supply Chain Performance
The implementation of the advanced inventory management solution yielded exceptional results:
- 98% On-Time Pick-Up Rate: Optimized scheduling and improved inventory management processes ensured timely pickups.
- 100% On-Time Delivery Rate: Real-time inventory visibility enabled seamless order fulfillment and delivery.
- Improved Production Scheduling: Accurate inventory levels reduced lead times and ensured uninterrupted production cycles.
- Stabilized Supply Lines: Enhanced coordination with suppliers ensured consistent inbound material flow, reducing disruptions.
Benefits of the Inventory Management Solution
The new warehouse inventory management system brought transformative benefits to the client’s operations:
- Reduced Stock-Out Risks: Real-time visibility minimized the risk of stock-outs and delays caused by misallocated inventory.
- Improved Operational Efficiency: Streamlined processes reduced costs and increased profitability margins.
- Enhanced Decision-Making: Up-to-date inventory levels empowered the inventory manager to make informed decisions, resulting in smoother operations.
Lesson Learned: The Power of Real-Time Inventory Visibility
This case study highlights the critical role of real-time visibility in inventory management in supply chain operations. A modern inventory management system not only provides accurate insights into inventory levels but also drives better decision-making, streamlines the order fulfillment process, and ensures operational success.
By prioritizing advanced inventory management solutions, businesses can achieve higher efficiency, lower costs, and improved supply chain performance. If your operations are facing similar challenges, take the first step towards transformation with a robust inventory management system.
Need Expert Logistics Advice?
Let’s optimize your supply chain for growth. Reach out to our experts today.
- contact@scsolutionsinc.com 616.554.8900 ext. 101
- Shipment Tracking tms@scsolutionsinc.com